Das rollende Automobilmuseum auf Tour
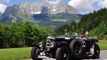
Die Türschweller des BMW 2000 haben besonders im vorderen und hinteren Endbereich starke Durchrostungen. Dass ein Rahmen oder eine selbsttragende Karosserie an tragenden Bereichen keine Durchrostungen zeigen dürfen, ist Voraussetzung dafür, bei der technischen Abnahme eine HUPlakette zu erhalten. Dabei sind fachgerechte Reparaturen an Rahmen und Schweller erlaubt. Pfusch, der sich etwa in mehrfach übereinander geschweißten oder auch nur eingenieteten Blechen manifestiert, wird vom technischen Überwachungsdienst natürlich nicht abgenommen.
Weg mit dem Schrott!
Da wir bei unserem BMW wirklich nur die Teile überholen möchten, die unwiderbringlich defekt sind, trennen wir am Schweller nur die Stücke heraus, die tatsächlich nicht zu retten sind. Der Schnitt wird genau im gesunden Bereich des Schwellers angesetzt. Doch bevor die defekten Stücke herausgetrennt werden, müssen wir noch Schablonen anfertigen. Die originalen Reste der Schweller und der inneren Versteifungen sollten so lange behalten werden, bis die Ersatzbleche fertig sind. Die alten Bleche dienen als Schablone für die neu nachgefertigten Ersatzbleche. Das Heraustrennen der Schwellerstücke erfolgt am besten mit einem Druckluft-Winkelschneider mit einer sehr dünnen Trennscheibe, denn es soll so wenig Material wie möglich verloren gehen. Je besser der Schnitt geführt ist, desto leichter wird es später, das Ersatzblech einzusetzen und anzupassen, ohne große Lücken am Stoß zu erzeugen.
Begonnen wird mit der inneren, kastenförmigen Rahmenversteifung über der Wagenheberaufnahme. Der Kasten ist ein rechteckig geformter Rahmen. Um die Seiten dieses Ersatzblechs abzukanten, werden zwei Winkeleisen in den Schraubstock gespannt. Das Blech wird entlang der Abkantlinie eingespannt. So können die nach innen geklappten Flügel abgekantet werden. Das Winkeleisen muss schmaler sein als die jeweilige seitliche Seite des Ersatzblechs. Im Schraubstock werden die letzten Flanken des Versteifungskastens umgeformt, bevor die fertige Versteifung probeweise eingesetzt wird. Als Nächstes folgt die doppelte Schwellerversteifung, die parallel zur äußeren Schwellerwand verläuft und eingearbeitete Versteifungssicken enthält. Mit einer Papierschablone wird die Form vorab angelegt.
Auf dieser Schablone werden auch die Sicken und der Verlauf der Mitte entlang der Rundung eingezeichnet. Diese Maße werden auf das Ersatzblech übertragen. An einem runden T-Amboss mit entsprechendem Radius wird nun das Blech mit einem Kunststoffhammer entlang der unteren Wölbung rund getrieben. Mit einem Stahlhammer würde sich das Blech beim Treiben über dem Amboss an den Treibstellen dehnen und damit leicht verziehen. Der Verzug könnte dazu führen, dass bei einer höheren Belastung das Blech knickt. Um der Schwellerversteifung noch mehr Stabilität zu geben, werden mit der Sickenrollenmaschine zusätzliche Sicken in das Blech gepresst. Mit einem Rundhammer werden die Enden der Sicken noch abgerundet und nachgetrieben.
Sobald die Wölbung und die Sicken fertig ausgeformt sind, werden die obere und die untere Kante der Versteifung abgekantet. Dies kann mit einer Abkantzange durchgeführt werden oder auch an einem scharfkantigen Amboss. Mit dem Hammer wird die Kante schrittweise umgetrieben, um das Blech nicht unnötig zu verziehen. Die innere Sickenversteifung ist nun fertig und kann fixiert werden. Doch erst wenn alle Teile angefertigt sind, werden sie endgültig verschweißt.
Innere Verstärkung bauen: Die Schwellerversteifung sitzt unter dem eigentlichen Türschweller und dient ganz wesentlich der strukturellen Stabilität der Karosserie.
Nachdem die alten Blechteile entfernt sind, wird zunächst eine möglichst exakte Papierschablone angefertigt.
Die Maße der Papierschablone werden anschließend auf das grob zugeschnittene Ersatzblech übertragen.
Das Blech wird jetzt auf dem Amboss mit passendem Radius mit einem Kunststoff-hammer grob in Form gebracht.
Nachdem die Wölbung hergestellt wurde, entstehen die Blechkanten im Schraubstock oder auf der Abkantbank.
Das Blech ist jetzt halb fertig und wird vor der wei-teren Bearbeitung am Fahrzeug auf Passgenauigkeit überprüft.
Die Sicken zur Versteifung des Schwellerbleches werden mit einer Sickenmaschine hergestellt.
Wer keine Sickenmaschine besitzt, kann die Versteifungen auch mit dem Hammer im Schraubstock erzeugen.
Das fertige Blech wird im Schweller ein-gesetzt und mit Haltepunkten oder Grip-zangen schweißfertig fixiert. Hier geht es zum Video!
Die Endspitzen des Schwellers
Auch der hintere Teil des Schwellers ist völlig weggerostet. Für die Reparatur müssen neue Ersatzbleche für die Endspitze im Radlauf und dem seitlichen Schweller angefertigt werden. Zuerst wird auf einem Papier die Schablone für das Ersatzblech an der Endspitze abgenommen. Das Blech wird etwas größer zugeschnitten, da die Kante später noch so umgeformt werden muss, dass eine Verbindung mit dem inneren Radlauf hergestellt werden kann. Auf einem Sandsack erhält das Blech mit einem Rundhammer die Grundwölbung. Unebenheiten werden mit einem Glättehammer auf einem abgerundeten Amboss geglättet. Wenn die Oberfläche gleichmäßig glatt ist, wird ein leichterer Glättehammer eingesetzt, um die Oberfläche nochmals feiner zu glätten.
Der letzte Feinschliff entsteht mit dem leichten Treiblöffel. Sie fragen sich jetzt sicherlich, warum so präzise gearbeitet wird. Dies hat nicht nur optische Gründe. Je weniger Unebenheiten das Blech aufweist, desto stabiler ist es im Falle eines Unfalls, da das Blech keine Sollbruchstelle aufweist. Deshalb ist genaues Arbeiten im Bereich der Schweller sehr wichtig. Gerade bei Fahrzeugen mit selbsttragender Karosserie müssen diese Arbeiten sehr penibel und korrekt ausgeführt werden. Die Rundung des inneren Radlaufs ist fertig. Nun wird die seitliche Sicke, die am äußeren Rand entlangläuft, in das Blech geformt.
Ein runder T-Amboss, der dem Radius der inneren Kante entspricht, dient als Treibunterlage. Zum Treiben wird ebenfalls ein Kunststoffhammer verwendet. Mit einem Stahlhammer würde sich das Blech während des Umformens strecken und deutlich verziehen. Nachdem die innere Form der Sicke am BMW abgenommen wurde, wird mit der Formenschablone die Rundung der Sicke und des Blechteils immer wieder überprüft, bis es perfekt passt.
Die Sicke ist aber immer noch nicht fertig. An einem etwas größeren runden T-Amboss wird nun der Rand nochmals mit dem Kunststoffhammer über den Amboss getrieben. So entsteht eine gegenläufige Wölbung zu der ersten Rundung. Nun kann das Blech angepasst und fixiert werden. Um es absolut passgenau fertigzustellen, wird noch die innere Kante zugeschnitten und mit einer Faltgabel abgekantet. Das Endstück des Schwellers im Bereich des Radlaufs ist fertig und kann fixiert werden.
Der Schweller wird geschlossen
Nun wird der letzte Teil des Schwellers angefertigt. Zuerst wird an dem noch vorhandenen Schwellerblech die Form mit einer Formenlehre abgenommen. Diese Schablone ermöglicht die passgenaue Nachfertigung des Ersatzblechs. Unter eine Stahlleiste werden zwei Blechstücke in der Stärke des Reparaturblechs gespannt und auf dem zugeschnittenen Ersatzblech alle Maße eingezeichnet, auch die Höhe der Knickkante im Schweller. Das Blech wird in die Blechschiene geschoben und entlang der Knickkante hochgebogen. Mit der Formschablone wird die Form immer wieder überprüft, bis sie perfekt passt. Nun wird mit der Schablone die Wölbung im Schweller abgenommen. Mit einem abgerundeten Treiblöffel wird auf dem Sandsack die Wölbung in das Blech getrieben. Sobald die Form erreicht ist, wird das Blech mit einem Treiblöffel auf einem Amboss geglättet und mit streichenden Schlägen vorsichtig glatt getrieben, um die letzten Unebenheiten zu glätten.
Da das Blech unter dem bestehenden Schwellerblech unterlappen soll, muss an einer Seite eine abgekantete Stufe erzeugt werden. Dies geschieht am besten an der Sickenrollenmaschine, bei der zwei stufenförmige Rollen aufeinandergesetzt werden. Im nächsten Schritt wird die untere Schwellerleiste um 90 Grad abgekantet. Nun wird auch die obere Kante des Ersatzblechs durch die Sickenrollen geführt und abgestuft. Das Blech kann nun erstmals angepasst werden. Damit in den Schweller eindringendes Wasser ablaufen kann, werden an der abgekanteten Unterseite mit einem Schraubstock und einem Finnenhammer noch zwei Sicken eingearbeitet. Dabei entsteht ein leichter Verzug, da das herausgetriebene Material die Unterkante zusammenzieht und verbiegt. Daher wird an der Streckmaschine das Blech entlang der Kante wieder etwas gestreckt. Um mehr Stabilität in die untere Kante zu bringen, wird der Rand noch einmal um etwa drei Millimeter abgekantet. Entlang der eingezeichneten Linie wird die Kante an einem Amboss mit dem Hammer umgetrieben und die Sicken werden mit einem schmalen Stahlstreifen nachgearbeitet.
Nun können alle Teile eingeschweißt werden. Doch beim Schweißen müssen einige wichtige Grundlagen beachtet werden, denn tragende Bereiche dürfen bei einer Reparatur nur nach bestimmten Vorgaben geschweißt werden. So dürfen die Stoßkanten der Rahmenhälften mit Schutzgas nur punktgeschweißt oder aber mit einem Widerstandspunktschweißgerät geschweißt werden. Hingegen können Nähte an eingesetzten Ersatzblechen auch mit durchgehenden Schweißnähten versehen werden.
Zwischen den einzusetzenden Teilen und dem vorhandenen gesunden Blech muss ein Verstärkungsblech eingesetzt werden, das zuerst mit dem bestehenden Rahmen punktgeschweißt wird. Dann folgt das Ersatzblech und anschließend wird die Naht geschweißt, entweder als Steppnaht oder durchgehend. Ist das neue Ersatzblech mit einer Abkantstufe versehen, entfällt die Blechversteifung zwischen den beiden Blechen. Um noch mehr über die Schweller Restauration eines BMW 2000 zu erfahren, haben wir eine Schritt-für-Schritt-Anleitung für Sie erstellt. Das dazugehörige Video finden Sie hier.
Schwellerblech herstellen: Da nur die Teile des Schwellers erneuert werden, die wirklich zerstört sind, fertigen wir die Bleche selbst an und verzichten auf fertige Reparaturbleche
Um das äußere Schwellerblech herstellen zu können, müssen auch hier zuerst die Kontur und der Radius abgenommen werden.
Der gewünschte Radius wird zunächst grob von Hand gebogen, eine Seite des Blechs sollte dabei eingespannt sein.
Mithilfe der vom Original abgenommenen Form wird der neu entstehende Radius so lange geprüft und bearbeitet, bis er passt.
Zum finalen Glätten des fertig gebogenen Blechs kommen der Sandsack und ein leichter Treiblöffel zum Einsatz.
Nun entsteht mit der Sickenmaschine (oder mit Hammer und Schraubstock) der Falz, mit dem das Blech am Schweller fixiert wird.
Das fast fertige Blech wird am Fahrzeug angehalten, um sicherzustellen, dass Radius und Falze stimmen.
Wenn das neue Blech passt, werden zum Abschluss noch zwei Wasserablaufsicken am unteren Rand ausgearbeitet.
Hier ist das fertige Blech mit richtiger Wölbung, passender Kante unten und den beiden Wasserabläufen zu sehen.
Nachdem das fertige Blech sorgfältig eingepasst wurde, kann es fixiert werden und ist damit fertig zum Einschweißen.
Schwellerendspitze erneuern: Die neue Endspitze entsteht durch das Treiben des zugeschnittenen Ersatzblechs mit einem Rundhammer über dem Amboss. Mehr zu diesem Prozess erfahren Sie in unserer Schritt-für-Schritt-Anleitung sowie in diesem Video.
Die Endspitze, also der Abschluss zwischen Innenkotflügel und Schwellerbereich, muss vollständig ersetzt werden.
Auch hier wird die grobe Grundform von einer Papierschablone auf das etwas größer zugeschnittene Blech übertragen.
Nun wird mit einem Rundhammer auf dem Sandsack begonnen, die Wölbung in das Blech zu treiben.
Die noch grobe und unebene Wölbung wird anschließend auf dem Amboss mit Glättehammer geglättet.
Das endgültige glatte Finish erhält die neue Endspitze durch sorgfältiges Bearbeiten mit dem Treiblöffel.
Im letzten Arbeitsschritt wird die Kante der neuen Endspitze mit dem Kunststoffhammer ins Blech getrieben.
Wurde sorgfältig gearbeitet, passt die selbst gefertigte Endspitze ohne Probleme in den Radkasten und kann verschweißt werden.