Oldtimer lackieren, aber richtig: Perfekte Vorbereitung ist das A und O
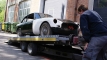
Alte Lagergummis, sei es ein Motorlagerblock oder die Gummibüchse in einem Querlenker, können im Lauf der Jahre steinhart werden, tiefe Risse bekommen oder einfach zerbröseln. All das ist nicht ungewöhnlich, da die Weichmacher des Gummimaterials über die Jahre „ausbluten“. Dadurch wird der Gummi hart und spröde, ähnlich wie das auch bei alten Reifen der Fall ist.
Harte Gummis im Fahrwerk wirken sich negativ auf die Fahreigenschaften eines Fahrzeugs aus, zu weiche und zerbröselte Gummis auch. Denken Sie an die Steuerung und an das Spurverhalten eines Oldtimers – da kann das zur Gefahrenquelle werden. Daher ist es ratsam, alte Fahrwerkgummis aus Lagern und Halterungen grundsätzlich auszutauschen. Bei einer technischen Abnahme kann wegen zu alter Fahrwerkgummis auch die Abnahme verweigert werden.
Sind alte Lagergummis erhalten, ist es durchaus möglich, nach diesem Abbild neue Gummis anzufertigen. Die einfachsten Methoden möchten wir hier aufzeigen. Suchen Sie sich aus den ausgebauten Lagern ein noch gut erhaltenes Exemplar, das Ihnen als Vorlage für die anzufertigende Gussform dienen soll.
Bei Lagern, in denen die Gummiteile bereits sehr rissig und rau geworden sind, kann mit Römer Plastilin (erhältlich in jedem Künstlerfachgeschäft oder im Spielwarenhandel) die Oberfläche des Teils für den Abguss geglättet und damit optimiert werden. Wichtig ist es, die Form so gut wie möglich zu replizieren, damit die spätere Gussform sehr genau wird.
Dazu wird das Plastilin sehr dünn aufgetragen und dicht verspachtelt. Das Plastilin füllt die Risse und glättet damit die Form. Fehlerhafte Stellen werden mit dem Plastilin ausgeglichen und wiederhergestellt. Mit einem weichen Pinsel, getränkt mit etwas Aceton oder Chloroform (erhältlich in geringen Mengen in der Apotheke), wird das Plastilin glatt gestrichen. Dadurch wird es kurzfristig sehr weich und flüssig und lässt sich damit präzise glätten und finalisieren. Wenn die Lösungsmittel verflogen sind, härtet das Plastilin wieder aus: Die Vorlage für den Formenbau ist damit fertig.
Der Formenbau kann auf unterschiedliche Art und Weise erfolgen. Die günstige Variante ist das Abformen in Gips. Dabei ist ein synthetischer Gips, wie Alabaster-Gips oder Dental-Hartgips, notwendig. Herkömmlicher Gips aus dem Baumarkt ist zu porös und deshalb für das Abgießen der Teile nicht geeignet. Das Elastomer, also das Gummilager, lässt sich daraus nicht mehr oder nur sehr schwer lösen, weil sich das Material mit der rauen Oberfläche des Baumarktgipses zu sehr verbindet.
Schwierigere Formen lassen sich nicht mehr öffnen. Zunächst wird eine Schale gebaut, in der das abzuformende Teil "schwebend" eingesetzt wird. Schrauben Sie das Mustergummi an eine der seitlichen Gussformwände. Unterhalb des Mustergummis muss etwas Spielraum sein, damit genügend Material für die Gussform darunter fließen kann.
Die dünnste Wand bei Ihrer Gipsform sollte mindestens 1,5 bis 2 Zentimeter betragen, damit die Gussform stabil bleibt. Mit dem Hartgips wird nun eine zweiteilige Form gebaut, ein Teil für die untere Hälfte der Abgussvorlage, eine zweite Hälfte für den oberen Teil. Achten Sie beim Anrühren des Gipses darauf, dass der Gips absolut blasenfrei ist.
In einen Becher mit lauwarmem Wasser gibt man genau so viel Gips, bis sich eine kleine Insel bildet. Diese Insel muss sich komplett mit Wasser voll saugen. Erst dann wird mit dem gleichmäßigen Verrühren des Gipses begonnen. So verhindern Sie Klumpenbildung.
Um Luftblasen zu beseitigen, wird die Rührschüssel entweder stark auf den Tisch geklopft oder auf den Teller eines Exzenterschleifgeräts (ohne Schleifpapier) gehalten. Die Vibration des Schleiftellers bringt die Luftblasen an die Oberfläche, wo sie durch kräftiges Blasen aufgelöst werden können.
Nach dem sorgfältigen Verrühren wird die Form genau bis zur Mitte mit dem flüssigen Gips aufgefüllt. Zeichnen Sie eventuell vorher auf dem Teil die mittige Trennlinie ein. Die Trennlinie sollte immer am höchsten Punkt einer Kurve liegen, damit es zu keiner Hinterschneidung kommt. Die Form wird nun etwas entlang der Formenwände geklopft, damit eventuell eingeschlossene Luftblasen aufsteigen.
Wenn der Gips gut ausgetrocknet ist, geben Sie etwas Sprühfett, Spülmittel oder Trennwachs auf die Flächen, damit sich später die beiden Gipshälften voneinander trennen lassen. Nun wird die zweite Hälfte gleichermaßen gegossen. Um die beiden Hälften voneinander unterscheiden zu können, kann in den Gips für die zweite Hälfte etwas Farbe beigemischt werden. Dies erleichtert später das Trennen. Wenn man nun die Form öffnet, erhält man eine negative Gussform für mehrere Abgüsse aus einer Gummivorlage.
Die zweite Variante, eine Silikonform, ist beständiger und kann öfter eingesetzt werden. Silikon an sich ist selber ein Elastomer und lässt sich dehnen. Damit stellen auch leichte und gröbere Hinterschneidungen kein Problem dar. Die Silikonmasse wird in einen Becher gegeben und mit einem Vulkanisator vermischt. Das Mischungsverhältnis entnehmen Sie am besten dem beiliegenden Begleitzettel. Erfahrungsgemäß ist das Anmischen aber auch ohne Waage möglich.
In jedem Gefäß sind es bei unterschiedlicher Menge an Silikonrohmaterial etwa zwei Millimeter Vulkanisator an der Oberfläche das richtige Mischungsverhältnis. Das Material muss sehr gut verrührt werden. Von dem Vulkanisator darf nichts mehr zu sehen sein und die Masse muss homogen wirken. Nun kann die Silikonmasse vorsichtig über den Rohling in die Form gegossen werden.
Da Silikonmaterial flexibel ist, kann dieser Abguss in einem Stück durchgeführt werden. Ein Schnitt an der Seite hilft bei der Entnahme des fertig gegossenen Teils. Um die Form geschlossen zu halten, reicht eine einfache Bandage aus Klebeband rund um die Form. Will man es ganz genau machen, erhält die Silikonform noch einen stabilen Stützmantel aus Hartgips.
Eine weitere Möglichkeit, eine genaue Gussform zu erhalten, ist die Fertigung von Negativformen aus Polyester. Diese Formen sind sehr lange haltbar und mit Sicherheit die professionellste Methode, eine Gussform anzufertigen. Zwei Möglichkeiten stehen hier zur Auswahl. Eine Form aus Polyestermasse oder aus Fiberglas.
Die Polyestermasse kann auch durch ein hartes Polyurethanmaterial ersetzt werden, was heutzutage die üblichere Form ist. Für die Anfertigung der neuen Lagergummis eignet sich am besten Polyurethan. Polyurethan ist ein Zweikomponentensystem, basierend auf einem Polyol und einem zugehörigen Härter. Beide Komponenten vermischt, ergeben nach der Reaktion miteinander einen stabilen Werkstoff.
Polyurethane können hart und spröde, aber auch weich und elastisch sein. Besonders Elastomere weisen eine vergleichsweise hohe Reiß- und Druckfestigkeit auf: ideal für hoch beanspruchte Fahrwerksteile. Ferner kommt es bei Teilen aus Polyurethan auf lange Sicht gesehen nicht zum Ausbluten des Weichmachers. Auch die Verformung des Bauteils unter Belastung ist wesentlich geringer als bei herkömmlichen Gummi.
Eine solche Polyurethan-Gummimasse auf Zweikomponentenbasis ist zum Beispiel Flexane (erhältlich bei Korrosionsschutz Depot www.korrosionsschutz-depot.de). Das Flexane-Material gibt es in drei Härtegraden mit der Shorehärte 40, 60 und 80. Die Shorehärte 60 ist in der Regel die richtige Wahl für Fahrwerkgummis. Die beiden Komponenten müssen exakt im vorgegebenen Gewichtsverhältnis sorgfältig gemischt werden.
Eine sehr genaue Waage hilft dabei, das richtige Mischungsverhältnis zu erreichen. Zuerst wird die Polylol-Flüssigmasse abgemessen. Diese Masse ist sehr zäh. Unter Zugabe des genauen Anteils an Härter werden die zwei Komponenten gut miteinander verrührt. So entsteht eine sehr homogene, flüssige Masse.
PU-Weich-Elastomere sind auch als klare Masse erhältlich. Diese können dann mit einem speziellen Farbkonzentrat in verschiedene Farben eingefärbt werden. Nach dem Anrühren wird die flüssige Masse in die Form gegeben. Lässt man die Masse in einem dünnen Strahl in die Form laufen, werden später keine Blasen in die fertigen Gummis eingeschlossen. Sehr wichtig ist es, die Form vorher noch mit Trennmittel auszustreichen. Dazu eignet sich zum Beispiel Silikonspray oder auch Formenwachs.