Oldtimer lackieren, aber richtig: Perfekte Vorbereitung ist das A und O
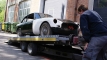
Es gibt etliche technische Schweißverfahren, die in der Automobilindustrie zum Verbinden von Karosserieteilen verwendet werden. Auch in der Hobby-Restaurationswerkstatt darf – spätestens wenn Karosseriearbeiten selbst erledigt werden sollen – ein Schutzgas-Schweißgerät (MIG/MAG) nicht fehlen.
Das MIG/MAG-Schweißen ist eine der einfacheren Formen des Schweißens. Weit mehr Übung erfordert das Autogen- oder WIG-Schweißen, bei dem Bleche mit einer Flamme aus Acetylen und Sauerstoff verschweißt werden. Das Lichtbogenschweißen mit einem elektrischen Schweißgerät sollte an Automobilen nicht eingesetzt werden; so hergestellte Schweißnähte werden in der Regel auch vom TÜV nicht als „fachgerecht“ anerkannt.
Das sogenannte MIG/MAG-Schweißen ist in der Autowerkstatt das populärste Schweißverfahren. Es wird vor allem beim Verschweißen von unlegiertem und niedrig legiertem Stahl, aber auch Aluminium, Kupfer oder anderen NE-Metallen eingesetzt.
Es gibt die unterschiedlichsten Preisklassen bei den MIG/MAG-Geräten. Wer das Schweißgerät öfter und langfristiger einsetzen möchte und Wert auf gute Arbeitsergebnisse legt, dem sei empfohlen, auf ein hochwertigeres Gerät zurückgreifen. Die Unterschiede zu günstigeren Geräten, wie man sie häufig in Baumärkten findet, fallen sehr bald auf. Bei einem qualitativ hochwertigeren Gerät lassen sich wesentlich mehr Einstellungen vornehmen, um eine perfekte Schweiß- oder Punktnaht zu erhalten. Hat das Gerät die Möglichkeit, Intervallschaltungen einzustellen, sind das ideale Voraussetzungen, um beispielsweise eine perfekte Punktnaht zu erhalten.
MAG steht als Abkürzung für „Metall Aktiv Gas" und bedeutet im Prinzip, dass das austretende Gas während des Schweißvorgangs das Schmelzbad vor dem Einfluss von Sauerstoff und somit vor der Oxidation schützt. MAG weist auf die Verwendung eines aktiven Gases hin. Fehlt das Gas, bildet sich ein Schweißpunkt mit sichtbarer Blasenbildung in der Schmelze, die sich mit dem Sauerstoff aus der Luft verbindet. Der Punkt oder die Schweißnaht wird extrem spröde und brüchig. Im Zentrum dieses Schweißpunktes beginnt der Punkt auf Dauer Feuchtigkeit anzureichern und dadurch zu rosten. Übrigens geschieht dies auch bei zu wenig Gaszufuhr.
Beim Schutzgas-Schweißverfahren (so umgangssprachlich der Begriff für das MAG-Schweißen) wird ein feiner Draht über eine Motorensteuerung durch einen flexiblen Schlauch zum Schweißbrenner geführt. An das Werkstück wird ein Massekabel angelegt und der Lichtbogen über eine Kontaktzündung mittels des dünnen Drahtes gezündet. Der Draht dient also als Elektrode. So bildet sich ein Magnetfeld mit einer induktiven Spannung. Es entsteht zwischen den beiden Polen (dem Blech als Masse und dem Draht als Pluspol) ein Austausch von Ionen in Richtung Masse und Elektronen in Richtung des Schweißdrahtes. An der Spitze des Schweißdrahtes entsteht ein Lichtbogen und die Schmelze für den Schweißvorgang.
Bevor man mit dem eigentlichen Schweißen am Werkstück beginnt, empfiehlt es sich immer, einige Testpunkte zu schweißen, um ein Gefühl für das Gerät und seine Einstellungen zu bekommen. Achten Sie darauf, dass das Gas aufgedreht ist und der Gasfluss genau auf die notwendige Menge eingestellt ist. Im Karosseriebereich bei Blechen zwischen 0,8 und 1,5 Millimetern liegt dieser Gasfluss bei etwa 8 Litern/Minute.
An jedem Gerät lassen sich vor allem zwei Grundeinstellungen vornehmen. Erstens die Stromstärke und zweitens der Drahtvorschub. Beide Einstellungsmöglichkeiten beeinflussen sich gegenseitig. Es gibt für das Schutzgas-Schweißen verschiedene Drahtstärken, doch in der Regel reicht der 0,6 Millimeter Draht für die Anwendung bei Blechen zwischen 0,5 und 2 Millimetern Stärke aus.
Um die richtige Einstellung zu finden, wird bei gleichbleibendem Drahtvorschub und unterschiedlicher Spannung jeweils ein Testpunkt geschweißt.
Der Drahtvorschub ist der erste Faktor, der einzustellen ist. Ist der Drahtvorschub zu gering eingestellt, schmilzt der Draht immer wieder ab, und es kommt zu keiner Schmelzbildung.
Stottert die Lichtbogenbildung bei gleichbleibendem Abstand des Brenners zum Werkstück, ist die Drahtförderung zu langsam. Das Schweißbild ist sehr unregelmäßig und nicht durchdringend.
Bleibt der Draht in der Schmelze kleben, ist die Drahtförderung zu hoch eingestellt.
Bei einem zu hohen Drahtvorschub drückt der Draht zu sehr in die Schmelze und entfernt damit den Brenner vom Werkstück. Ist der Abstand des Brenners zu der Schmelze zu groß, wirkt das Schutzgas nicht mehr ausreichend.
Wichtig ist es auch, die Rückbrennzeit nach dem Abbruch des Schweißens zu beobachten. Der Draht sollte nicht zu weit nachlaufen, da er ansonsten in die Schmelze eintaucht und in der Schmelze hängen bleibt.
Ist der Drahtvorschub optimal eingestellt, beginnt man mit einer niedrigen Spannung und erhöht diese stückweise. Ist die Spannung zu niedrig, zündet der Lichtbogen nicht richtig, und die Schmelze bleibt sehr oberflächlich und dringt nicht in das Blech ein. Ist die Spannung zu hoch, schmort das Blech sehr schnell durch, oder es bildet sich ein sehr breit verlaufendes und hohes Schmelzbad. Ein solcher Punkt ist zwar stabil, aber er ist kosmetisch nicht sehr gut wegzuschleifen.
Am idealsten ist ein Punkt, der flach liegt und tief durchgedrungen ist. Ist der Punkt regelmäßig zerflossen und besitzt einen leichten Krater in der Mitte des Punktes, ist der Schweißpunkt gelungen. Dies ist bei richtigen Einstellungen nach etwa 3–4 Sekunden der Fall. Auf der Rückseite lässt sich bei einem gut gesetzten Schweißpunkt ein leichter Punkt mit einer Aura erkennen. Diese Verbindung ist stabil und hält auch stärkere Belastungen aus.
Das Ergebnis steht aber auch in der Abhängigkeit zur Stellung des Schweißbrenners. Die Schweißdüse wird beim neutralen Schweißen in einem Winkel von 90 Grad, im Falle des „stechenden Schweißens“ im Winkel von etwa 80 Grad zur Schweißebene gehalten. Der Abstand beträgt in etwa das 10-fache des Schweißdrahtes, also bei einem 0,6-Millimeter-Draht etwa 6 Millimeter. Es gibt drei verschiedene Stellungen des Schweißbrenners.
Üblicherweise verwendet man vor allem beim Punktschweißen die neutrale Stellung: Der Draht wird senkrecht auf den Punkt zugeführt. Es ergibt sich ein kleiner runder Punkt mit einer flachen Krone. Dies wirkt sich auch bei einer gezogenen Naht ähnlich aus. Die Naht ist schmal und flach, auf der Rückseite ist eine schwache Naht mit einer Aura zu erkennen.
Die zweite Technik ist die gezogene Stellung. Der Brenner wird über das Blech gezogen. Dabei entsteht ein sehr hoher Punkt mit einer tiefen Einschmelze. Auch bei der gezogenen Naht ist eine hohe Naht mit einer tiefen Schmelze zu erkennen. Diese sieht man deutlich auch auf der Rückseite.
Die dritte Stellung des Schweißbrenners, als stechend bezeichnet, ist die gängigste bei der Arbeit an der Karosserie. Solche Schweißnähte sieht auch die technische Abnahme am liebsten. Bei Punktnähten erkennt man einen flachen Punkt mit einer leichten Durchschmelze. Maßgeblich für ein gutes Schweißresultat ist auch der Kontaktrohrabstand. Dieser Abstand bestimmt bei dem Schutzgasschweißen den Widerstand der stromführenden Drahtelektrode. Ein zu großer Abstand des Kontaktrohres zu dem Werkstück führt zu einer zu geringen Induktionsspannung und damit zu einem zu geringen Einbrand der Schmelze.
Ist das Kontaktrohr zu nah am Werkstück, brennt sich die Schmelze zu stark ein. Einen zu großen Kontaktrohrabstand erkennt man übrigens an der extremen Spritzerbildung. Bei zu geringem Abstand erkennt man relativ schnell einen zu großen Abbrand.
Beachtet man all diese genannten Grundfaktoren, steht einer stabilen und TÜV-tauglichen Schweißnaht oder Karosserieverbindung nichts mehr im Weg.